An Automated NSW Smart Solutions Guide
The call came in on a rainy Friday evening – the kind of call no project manager wants to receive.
“I have some bad news,” the voice on the other end said. “The new air handler is missing its supply air temperature sensor and the power supply for the controller is burned up.”
This was bad news, but we didn’t know yet that the onboard controller hadn’t even been configured to communicate with our networked control panel. The supply chain was already a mess, it was four days before Christmas, and the clock was ticking on our time-critical project.
When the Schedule Leaves No Room for Error
Replacing large equipment like air handlers during a manufacturing shutdown requires a certain amount of belligerent optimism. When the customer’s employees take the week off and production ceases, a race against time begins. The project’s Gantt chart looks nearly vertical as activities and trades stack on top of each other in the same physical space:
- Annual maintenance crews performing their checks
- Contractors taking down and putting up walls
- Teams re-sealing floors
- Equipment installers placing new units
- Pipe fitters running connections
- Electricians pulling wires
- Sheet metal workers rerouting ductwork
- Technicians performing checkouts and testing
There’s simply no room for delays – the facility must resume production by a specific date. Every hour of downtime represents lost revenue for your customer.
The Time-Saving Benefits of Factory-Mounted Controls
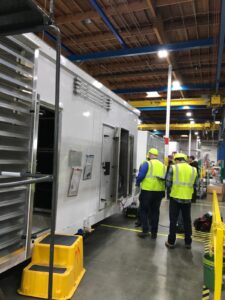
When you’re installing controls on a job with such a tight schedule, factory-mounted controls can give back that most precious resource: time.
Factory-mounted controls allow the control’s work to begin before the equipment even ships to the site. This means your controls contractor can address any issues or delays before they impact the critical project timeline.
The unit controller can be installed, partially wired, and programmed while the air handler is still on the factory floor. Point-to-point checkout and preliminary operational tests ensure sensors are wired and scaled properly, power supplies are functioning correctly, and the controller is pre-loaded with the necessary programming.
When the crane sets the unit on your rooftop, it’s nearly ready to go. All that remains is completing the wiring and testing of remote sensors, performing any required functional or performance testing, and confirming communication with your site’s BAS.
Don’t Count on Christmas Miracles
In our case, we got lucky with scrounged parts from other jobs and a supertech who knew both the default password AND how to configure the on-board controls. But you never want “Christmas Miracle” to be a subtask in your project schedule.
Factory-mounted controls provide flexibility in your project timeline and eliminate potential points of failure during installation. They ensure that when equipment arrives on site, it’s ready for quick integration into your system – no miracles required.
For critical manufacturing facilities where downtime means lost revenue, this approach doesn’t just save time – it provides peace of mind that your automation system will be up and running when production needs to resume.
Next time you plan a tight-timeline project, consider making factory-mounted controls part of your specification. Your future self (especially the one answering emergency calls on rainy Friday evenings) will thank you.